ITER sets new challenges for leak detection
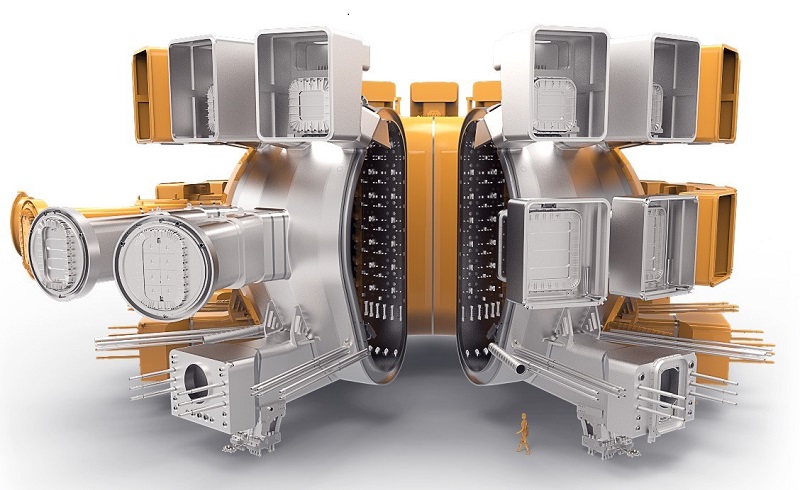
ITER’s vacuum vessel must be kept under ultrahigh vacuum to maintain the right conditions for fusion (Courtesy: ITER) © Retrieved from https://physicsworld.com/
40-30, a French company that specializes in process and vacuum technologies for large engineering projects, has been a long-time supplier to the ESRF and other major experimental facilities. That includes ITER, the fusion reactor now being built in Cadarache in the south of France, where 40-30 is part of a consortium designing and building one of the most complex leak detection systems in the world.
Achieving and maintaining the right conditions for the fusion reaction between deuterium and tritium requires the vacuum vessel that contains the plasma, along with the 14,000 m3 cryostat and other core components, to be kept under ultrahigh-vacuum conditions. Any leaks or contamination must be detected as soon as possible, but that’s a challenging task when there are around 2000 entry points to the overall system.
“We spent a whole year working out the basic functional requirements of the leak detection systems for ITER, and translating them into technical specifications and contract documentation,” says Roger Martín, the project manager at Fusion for Energy (F4E) who was responsible for procuring the detection system.
The resulting design is a series of helium leak-detection subsystems that exploit high-resolution mass spectrometry to detect helium ingress under specific conditions – including a high-radiation environment with strong magnetic fields, complying with the nuclear safety standards applying to ITER, and even the possibility of seismic activity. Although mass spectrometry is widely used for leak detection, adapting the technology to ITER standards is particularly demanding.
After an extensive tendering process, the €17 m contract for delivering the leak-detection system was awarded to the IG4 consortium, led by Spanish engineering consultants IDOM. 40-30 will be responsible for process and vacuum engineering, as well as equipment specification, while Gutmar will manufacture, assemble and test the equipment.
“We are really proud to be involved in this project,” says Charles Agnetti, CEO of 40-30. “For this mission, 40-30 has assigned its most experienced specialists in vacuum technology and processes, leak detection and gas analysis.” It will take more than three years to deliver the project, with a preliminary design review due in the first half of 2021.
Last News
Préventica 2024
40-30 and Riken Keiki at Préventica 2024, October 8 & 10, 2024 at Eurexpo Lyon.
V2T 2024
40-30 at the 2024 Vacuum Technologies for Tomorrow (V2T) in Grenoble WTC Congress Center on May 29 & 30, 2024.
SEMICON Europa 2022
Visit us at SEMICON Europa 2022 in Munich, from 15th to 18th of November. Visit us at our booth C1-465.